Wednesday, December 01, 2010
Published!!!!
Tuesday, November 30, 2010
Subversive Stitchers: Women Armed with Needles: Good Advice from a Real Professional Artist: Susan Lenz
Subversive Stitchers: Women Armed with Needles: Good Advice from a Real Professional Artist: Susan Lenz
Got to love the blog title. But seriously, the points Susan Lenz brings up are oh so valid. Work worth doing is worth doing well, and I need to remember that, and put the time in that my art needs and requires of me.
Saturday, November 20, 2010
Polyester references
In the books I have in my stash, there are three references to dyeing polyester:
- Brackmann, Holly ‘The Surface Designer’s Handbook’ – chapter 7
- Dahl, Carolyn ‘Transforming Fabric’ – chapter 8
- Proctor, Richard M, and Jennifer Lew ‘Surface Design for Fabric’ – page 42 - 43
Caryl Hancock also posted to the DyersList and kindly allowed me quote her:
I have two more sources for information on disperse dyes: the first is a book by Linda Kemshall, "Color Moves, Transfer Paints on Fabric" published by That Patchwork Place (Martingale?), C. 2001. Explains a lot of the ways to "play" with these dyes. (http://www.amazon.com/Color-Moves-Transfer-Paints-Fabric/dp/1564773418/ref=sr_1_2?s=books&ie=UTF8&qid=1290198560&sr=1-2) Under $10.Thanks, Caryl!
![]()
The second is a booklet by Jan Beaney and Jean Littlejohn, "Transfer to Transform." This is one of their earlier booklets (about 20 pages, I think) and is available from Quilting Arts or Amazon $16-21. There is nothing in the notes from the 2 classes I have had with Lisa [Grey] about other reference books; she probably knows the most of just about anyone about these dyes, and is a great teacher.
I also saw that there is a disperse dye class being offered at the SDA conference in Minneapolis next June.I have also purchased some of the colors from ALJO (http://www.aljodye.com/main.html) that are different from what Pro-Chem offers - no affiliation.
I use disperse dyes in printers. I buy them from Sawgrass. Sawgrass Inks also has a textile ink that prints from epson printers - the 4000 series prints 17" wide. http://www.sawgrassink.com/ they sell both desk size and large format printers, equipment and supplies. Conde Systems is another good supplier.
Jaquard also has dyes filtered very fine for printers. since they are acid and reactive dyes they need to be steamed - whereas textile pigments do not. disperse dyes need a heat set but not necessarily steam.there is a lot of information out on disperse dyes in printing presses. I mentioned sawgrassink before in another reply, and conde systems. They are also known as sublimation inks to printers. If you google sublimation inks you will find quite a bit.
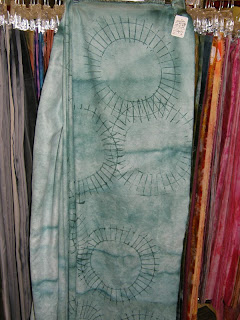
And Nancy Evans came up with another reference -
Below is a cut and paste from Pro Chemical’s Product Instructions page.
Imagery on Fabric by Jean Ray Laury also has a section on disperse dyes as well as transfer papers (which is just paper that is coated with disperse dye). A couple of times, I've lucked into acquiring some transfer papers, and they are fun to play with - got them at a thrift shop and a fabric store that holds onto everything it ever carried - nothing is clearanced! My good fortune to find them. I find the transfer papers are much more intense than the papers I paint with the disperse dye. Might be a function of how I've mixed? I do try to follow directions tho.... so maybe the papers are just brighter. ---nanThanks to you too, Nan!
I have learned a lot from Lisa Grey through a few emails and a phone call. Here’s a link to her class description: http://www.lisagrey.com/Lisa_Grey/Printing_DD.html - be sure to click on the “student work” link at the bottom.PRO Disperse Dyes Designed to permanently dye synthetic fibers -- in particular polyester, acetate rayon, nylon, and acrylic. Solid shade dyeing is done at a boil. A swelling agent, PRO Dye Carrier NSC, is necessary for the dye to penetrate polyester fiber.** Acrylic fibers do not dye dark; expect to achieve a pastel depth of shade only. Two ounces (58 gm) of dye powder will dye 25 lbs (11 kilograms) of polyester to a medium shade in a solid shade dye bath. Available in 13 intermixable colors. Note: many polyester and polyester-cotton fabrics have a permanent press finish. This must be removed before successful dyeing is achieved.
Transperse Transfer Printing Dyes - Your best choice for transfer printing on polyester and poly blends. Available in 9 intermixable colors.
And don't miss the work of Barbara Barrick McKie at http://www.mckieart.com/!
>
**I have never done any of my polyester this way. It is all direct application of dyes, either regular or thickened, allowed to dry and heat pressed. The thickened dye is more frugal – all the color is on the ‘right’ side (important with NuSuede), with the back remaining white. I also don’t do heat transfers, because I do 3 – 4 yard pieces and want fairly consistent results. Have yet to do any screen printing – I’ve never gotten into that.
Friday, November 19, 2010
Reviews and Previews
Hard to believe 6 weeks have passed since I last posted. If troubles come in threes, we’ve had it for a while. After the bad brake incident in September, we came home to a hole in the roof, with water running down from the third floor to the entrance hall. Yuck. Got it fixed (there went any profits,) and a couple weeks later the heater started making loud noises and shooting flames. Well, it was about 55 years old, like us, and that’s a pretty long time for a boiler. In the picture at right, the covers were removed for the funeral. It didn’t run like that all the time. Anyway, it got kicked to the curb and a new Energy Star gas unit has been installed. What a difference – and the basement smells much better! Plus, I will have more and hotter water for washing out MX dyes.
We did a total of six shows this fall; still haven’t crunched all the numbers, but it’s time for some other source of income. My current plan is to do the spring shows in Hampton, VA, Somerset, NJ and Lancaster, PA, and then probably no shows except Oaks, since it’s 20 miles away, until (drumroll) Houston, next fall. I spent almost as much to do the show in Chantilly, VA this fall, with the poorest results of any show. It was a good opportunity to have a different set-up (see picture.) The ladies from Quilters Remedy and I had our booths side-by-side, and we each had a cross-aisle next to us, so we both had corner booths.
Thanksgiving is a week away and as always there’s a lot to be thankful for. I’m thankful for all the opportunities that have come my way this year, and all the wonderful people I’ve met along the way. I’m thankful for the optimism necessary to keep trying for a while longer, and for the common sense needed to realize that some sort of ‘Day Job’ is necessary too. I’m very thankful that I won a ribbon at the Oaks show, and have the snow-dyeing article coming out next month in American Quilter! (Both of those actually came with a check!) Now I have to get more work done, including posting lots more fabrics on the website, and upgrading my inventory without spending a lot more money!
Snow Dyeing!
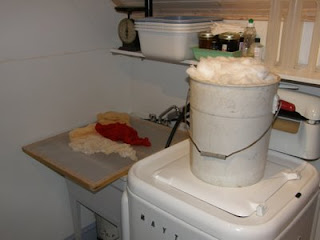




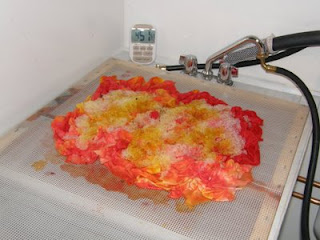

7 comments:
- Deb said...
-
Love the snow dyes! It does make me think I'd like to try and especially love the grid marks from the board underneath!!! I live in the south, so this is a limited opportunity for me. I may get the equipment ready and see if we get a rare snow storm for me to try it. For our usual snow storms check out my recent posting in my blog http://debharwell.blogspot.com/
- Thursday, January 29, 2009 2:51:00 PM GMT-05:00
- Karen said...
-
It turned out great, good job, neat seeing the grid pattern on the fabric. That happened to me once with a golf ball (don't ask).
Karen - Thursday, January 29, 2009 4:09:00 PM GMT-05:00
- Anonymous said...
-
this is cool lisa! i am definitely going to try this out (sooner or later). we have plenty of snow but it is unfortunately buried under a good piece of ice. sort of like creme brulee on a large scale.
Rita from Scranton - Friday, January 30, 2009 8:08:00 AM GMT-05:00
- I'm Bobbie said...
-
Love your pieces! Thanks for your comment on my blog. Yes, I've been to the Barn many times, all of Carol Soderlund's classes plus more. Bet we've been there at the same time.
Keep up the great blog! - Tuesday, February 3, 2009 3:05:00 PM GMT-05:00
- Judy said...
-
lovely snow dyeing.......pity I live in GA where we rarely have any snow at all!
- Sunday, February 15, 2009 10:18:00 AM GMT-05:00
- Sue said...
-
Your fabric is very, very pretty. Thanks for blogging about it. I have a question though. Do you think the results are significantly different than doing low immersion dyeing and really good scrunching? Just curious, as I've not done it.
Sue - Sunday, February 15, 2009 10:42:00 AM GMT-05:00
- Lisa in Penna said...
-
Hi Sue - The finished product is rather different from traditional scrunching. Two of the fabrics were already dyed a very pale orange, but the sateen that started out white doesn't have any white areas remaining. They are pale yellow at the lightest. Also, there isn't the usual crystalline patterning from LWI. All the edges are softer. Jane Dunnewold described this as 'snow resist' dyeing, and I think that the gradual combination of dye and fabric does lead to a different result. I'd like to hear what other folks think! - Lisa
- Sunday, February 15, 2009 9:28:00 PM GMT-05:00
Links to this post
- Färben im Schnee
- 1. Schnee vom Gestern Des öfteren bin ich gefragt worden, ob ich schon im Schnee gefärbt hätte. Gereitz hat es mich schon lange. Gestern habe ich es endlich probiert, Schnee gibt es ja momentan genug. In Quilting Arts Nr. ...
- Posted by Helena at Friday, January 15, 2010 4:50:00 AM GMT-05:00
Thursday, October 07, 2010
Back home – another interesting week
Once we got over the whole problem with the brakes, we went on to vend at three shows in three weeks. Oaks, PA (see below), Chautauqua, NY and Chantilly, VA. As usual, we learned from every experience; the big lesson this fall has been to cut the overhead as much as possible. That means we need to sleep and eat cheaper. We got a microwave and TV dinners; to do that better we need to get the TVDs the day they’ll be eaten, not before. Pop Tarts still taste good when the hotel doesn’t have breakfast.
Got home on Sunday; then had to deal with the credit card issue and do household chores on Monday and Tuesday. Then Wednesday I headed down to Philly to report for jury duty at the Federal courthouse. Took the train to get there, and got a copy of the sports pages from the lady in front of me. That kept me busy in the assembly room, because I wasn’t smart enough to change scissors in my sewing bag. However, it took three guys to get them off me! And yes, I am back working on appliqué. Nothing like a little positive reinforcement for motivation. There’s a picture of the block below – it’s one of 256, and I’m halfway there. When I got home from the city (not selected), I sat back, watched Roy Halladay pitch his no-hitter and stitched. Aaahhhhh . . . . .
There’s an appliqué class this Monday evening (the 11th) in Red Hill – you can sign up at DippyDyes.com if it’s your first time. Thanks!
My Customers are the Greatest!
This is to thank all the folks who purchased items from me at the recent fall shows. I especially want to thank the customers in Chantilly, VA who paid with credit cards. My charge card machine gave up the ghost after the show, so I had to call everybody to get their information again. Everybody gladly helped out, so I didn’t lose any of those sales, and on top of that, I had some really nice conversations with several of them. So, thanks again to everybody!
PS - I should also mention that the new machine is on its way, just in time for the Berks Quilters Guild show in Leesport. Nobody needs to worry about using a credit card with me in the future!
Wednesday, September 15, 2010
Bad brakes and the happy dance!
OK, the day didn’t start out quite as planned. Had to wait for the UPS driver so I could sign for a package. Then it was off to the show in Oaks. Well, the pesky idiot light on the dashboard wouldn’t go out – it was the brake light. Not something to ignore! Problem is, the van was completely loaded with fabric and fixtures. Exquisitely loaded, if I may brag on hubby. So, back home, load everything into the pickup truck, with the fabric on the bottom, and follow the van to the garage. Shout-out to Scootie’s garage – Ken came back after his dinner to replace the ruptured brake line(s). Get that man a pickle! Finally, two hours after we first set out, we headed down to the show.
Then things started to improve. After beginning to unload, a spot at the door opened up, and we grabbed it. Unloading proceeded well, and at least it’s a beautiful day – no rain on the goodies. Everything came into the booth, and DH took a break. So, en route to the restroom, I decided to check out some of the quilts. There was a list of winners there and – shriek – I won!!!! Here’s a picture:
That’s it for tonight – very pleased about the quilt, AND that it wasn’t raining, AND that we were only blocks from home, going slowly in the van. See you at the show!
Tuesday, September 14, 2010
More Discharge
Here are a few more discharged fabrics that I have produced lately. I think they look different than the other ones I’ve posted recently. The first one is a 44” square of broadcloth dyed a fairly dark blue-green. It was then accordion-folded in two directions and clamped between 4 CDs. Then it was discharged in Thiox and overdyed with yellow and red.
The second piece started out as a grey-green color. Then it was bound in the ‘onion bag on steroids’ and discharged, then overdyed with brown. The patterning from the netting isn’t as strong as some other, but it does evoke stone very will.
The last piece is a square of sateen that was also dyed a dark blue-green. It was folded in an arc shape from one corner, clamped and discharged. No overdye on this one – it works as it stands. Thanks for looking!
Wednesday, August 11, 2010
A blast from the past
Digging through some junk boxes the other day, I came across a love letter from my Mom to my Dad. It was dated December 1 through 4, 1944, when he was in the Army, and two years before they were married. She would have been 27, he, 31. The following segment caught my eye:
Saturday finished, almost completely, my Christmas shopping & then met Mother. She and Dad are giving Fred[erika – Mom’s twin sister] & Tom bedside tables for Christmas & they wanted to give me an equivalent present, so I was to buy “a couple of tables’ worth of dress – “ or in other words, a very “yummy one.” We had no luck at our usual pet place & then went to another we like, a little place, & they had several pretty ones. I brought 2 home to “model'” for Dad – I am to have one & I think they may be giving Fred the other, of black wool jersey. The one I’m to get is so pretty – I just want to go & feel it from time to time & can hardly bear not bubbling about it to Fred. It’s a two-piece dress – really an unlined-jacket suit – of soft, light black wool, with a one-button-at-the-waist closing. Then into the front is stitched a very pretty crepe vest of pink, trimmed with black sequins (paillettes) & beads, & tied at the neck. It is lovely – will be nice for holiday festivities & theater later, & still later, with a frilly blouse will be perfect for spring. I “love it good,” as Mary Lib would say – now if I could just ‘doll up” in it & meet you at the airport like one Christmas evening -- -- !
This ended up being two full pages out of the 17 she wrote! It made me smile for several reasons: while he may have enjoyed a slice of home life, I doubt he cared that much about a dress. But mainly I smiled because she sounds like every textile person I know . . . ‘I just want to go & feel it from time to time’ are words I’ve heard more than once at a quilt show! Hope you enjoyed it too!
Tuesday, July 20, 2010
More on the Keeper
Well after reviewing all the wonderful comments on ‘Can’t let this one go,’ below, I decided it was time to do some virtual design wall stuff. Plus it’s a good way to learn to mess with Photoshop Elements and DrawPlus Starter Edition. Not going to post everything I tried; the items below were worth keeping. Some I like better than others – what do you think?
Wednesday, July 14, 2010
More on the booth; life moves along
Life continue to move on, as life is wont to do. I've sent off my article on snow-dyeing to American Quilter magazine, and they asked that I take down the parts of my blog that overlap the article. So I've done that; but I've saved them locally, so they’ll be back next year. I'm just about to ship a big box of samples to them - the Editor, Chris, is going to select from them and they'll take professional photographs of the fabrics. It's all very exciting.
Today I also went to a temp agency to try to line up some work between now and the fall shows. Hope something comes of that - it will mean less time, but a little more money in the bank. And I'm still adding items to the website, and there's a lot to add!
Two weeks ago we set up at the York PA Guild show, and I tried out the new garment racks. It made the fabrics a lot more accessible; here's a picture:
Saturday, July 03, 2010
Cloud Photos Challenge
Hello, quilting friends, textile tootsies and dye junkies! On the QuiltArt email list lately there has been some discussion of cloud photos, copyright free and otherwise. I thought to myself ‘Why not just send her your pictures? Nothing to be afraid of, right?’ Then I decided to go one step further and make a challenge out of it. Below are six photos I took a bit over a year ago, June 2009. My challenge to you is to create a piece of textile art, whether a quilt, complex cloth, clothing, object, vessel, weaving, whatever, inspired by these photos. Anything goes – you can print them on cloth, manipulate them any way you like, create a meditation; use stitching, beading, recycled materials – ANYTHING! And as an incentive, I will award DippyDyes gift cards to the three I judge to be the best. Nothing massive, sorry, probably $32 for first place, $24 for second, and $16 for third. And since this is all about me, the deadline is my birthday, September 7, just before I head out to a lot more shows.
More details will be forthcoming once I figure them out. These pictures are available for your personal, non-mass-market use. If you do sell, show, or otherwise profit from them, please just give me credit in the caption. If you are going to make 10,000 coffee mugs out of them, that’s another story! If you need larger, higher-resolution images, let me know.
About the clouds: I believe these are mammatus, or mammatocumulus clouds. It was fun to photograph them; the first two pictures were taken from the studio window, then I followed the group of clouds on foot; by the last picture the structure had pretty well broken up.
Wednesday, June 16, 2010
Polyester - not an original thinker!
Tuesday, June 15, 2010
Polyester Sunprint
Couldn’t wait to process this piece of Nu-suede. It’s my first effort at a sunprint. Looking at it critically, there are several flaws – boring, all-over placement of the leaves, a thread visible in the upper right of the detail, below, and general blurriness. Also, monochromatic doesn’t do much for it. But it’s still extremely cool and I can’t wait to do more, and do it better!
Thursday, June 10, 2010
Auditioning Paintstiks
Well, I have been giving some thought to the ‘keeper’ fabric and came up with a decent way to audition Shiva Paintstiks. This illustration shows about the third iteration, and the first I like. The paint for now is temporary – I applied it to Glad Press ‘n Seal™ cling wrap - you can see it best around the top fan. Once the paint has dried thoroughly, I can remove and reposition it all I need. I like how the curvilinear shape of the fans echoes the bound spider webs. Hope you do too. I did test out some intense green, but that might be best in very small bead-sized doses. Thanks for looking!
Monday, June 07, 2010
Pleasures of Polyester
Well, my new shipment of PFD and dark fabrics arrived today from Robert Kaufman. The big ticket item is 100 yards of their 100% polyester Nu-suede fabric. It feels like a moleskin and does fray a bit. But is so very soft and luscious – it looks like a great fabric for warm blouses or else jacket/skirt/slack combos. Yes, garment sewing. Good thing my best friend taught sewing for 30 years! Here are a couple pictures of work in process and finished goods from the first 30 yard roll:
Started the first piece with an all-over pink color, then rag-rolled an 'orange creamsicle’ color over it.
The second piece shows a yard of fabric in process. It got turquoise dye (Pro-Chem’s Transperse turqouise) all over, then it was spread out on plastic (my favorite heavy vinyl from Jo-Ann’s.) Then I sprinkled it with salt and waited for it to dry. That piece sold right away, so I did it again with a three-yard piece, which is shown in the third photograph. That shows it mid-way through the heat-press process, which is when the color changes. Transperse is Pro-Chem’s name for their disperse dyes designed for transfer printing. The main problem with the whole process is the investment into the heat pr
ess. But everyone who handles the fabric falls in love with it – I did!
I still have more to learn, so I’d better get to it! Thanks for looking!