Tuesday, November 30, 2010
Subversive Stitchers: Women Armed with Needles: Good Advice from a Real Professional Artist: Susan Lenz
Subversive Stitchers: Women Armed with Needles: Good Advice from a Real Professional Artist: Susan Lenz
Got to love the blog title. But seriously, the points Susan Lenz brings up are oh so valid. Work worth doing is worth doing well, and I need to remember that, and put the time in that my art needs and requires of me.
Saturday, November 20, 2010
Polyester references
In the books I have in my stash, there are three references to dyeing polyester:
- Brackmann, Holly ‘The Surface Designer’s Handbook’ – chapter 7
- Dahl, Carolyn ‘Transforming Fabric’ – chapter 8
- Proctor, Richard M, and Jennifer Lew ‘Surface Design for Fabric’ – page 42 - 43
Caryl Hancock also posted to the DyersList and kindly allowed me quote her:
I have two more sources for information on disperse dyes: the first is a book by Linda Kemshall, "Color Moves, Transfer Paints on Fabric" published by That Patchwork Place (Martingale?), C. 2001. Explains a lot of the ways to "play" with these dyes. (http://www.amazon.com/Color-Moves-Transfer-Paints-Fabric/dp/1564773418/ref=sr_1_2?s=books&ie=UTF8&qid=1290198560&sr=1-2) Under $10.Thanks, Caryl!
![]()
The second is a booklet by Jan Beaney and Jean Littlejohn, "Transfer to Transform." This is one of their earlier booklets (about 20 pages, I think) and is available from Quilting Arts or Amazon $16-21. There is nothing in the notes from the 2 classes I have had with Lisa [Grey] about other reference books; she probably knows the most of just about anyone about these dyes, and is a great teacher.
I also saw that there is a disperse dye class being offered at the SDA conference in Minneapolis next June.I have also purchased some of the colors from ALJO (http://www.aljodye.com/main.html) that are different from what Pro-Chem offers - no affiliation.
I use disperse dyes in printers. I buy them from Sawgrass. Sawgrass Inks also has a textile ink that prints from epson printers - the 4000 series prints 17" wide. http://www.sawgrassink.com/ they sell both desk size and large format printers, equipment and supplies. Conde Systems is another good supplier.
Jaquard also has dyes filtered very fine for printers. since they are acid and reactive dyes they need to be steamed - whereas textile pigments do not. disperse dyes need a heat set but not necessarily steam.there is a lot of information out on disperse dyes in printing presses. I mentioned sawgrassink before in another reply, and conde systems. They are also known as sublimation inks to printers. If you google sublimation inks you will find quite a bit.
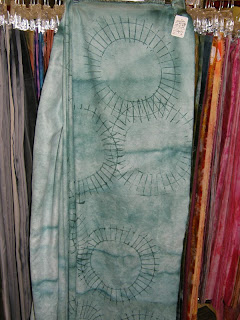
And Nancy Evans came up with another reference -
Below is a cut and paste from Pro Chemical’s Product Instructions page.
Imagery on Fabric by Jean Ray Laury also has a section on disperse dyes as well as transfer papers (which is just paper that is coated with disperse dye). A couple of times, I've lucked into acquiring some transfer papers, and they are fun to play with - got them at a thrift shop and a fabric store that holds onto everything it ever carried - nothing is clearanced! My good fortune to find them. I find the transfer papers are much more intense than the papers I paint with the disperse dye. Might be a function of how I've mixed? I do try to follow directions tho.... so maybe the papers are just brighter. ---nanThanks to you too, Nan!
I have learned a lot from Lisa Grey through a few emails and a phone call. Here’s a link to her class description: http://www.lisagrey.com/Lisa_Grey/Printing_DD.html - be sure to click on the “student work” link at the bottom.PRO Disperse Dyes Designed to permanently dye synthetic fibers -- in particular polyester, acetate rayon, nylon, and acrylic. Solid shade dyeing is done at a boil. A swelling agent, PRO Dye Carrier NSC, is necessary for the dye to penetrate polyester fiber.** Acrylic fibers do not dye dark; expect to achieve a pastel depth of shade only. Two ounces (58 gm) of dye powder will dye 25 lbs (11 kilograms) of polyester to a medium shade in a solid shade dye bath. Available in 13 intermixable colors. Note: many polyester and polyester-cotton fabrics have a permanent press finish. This must be removed before successful dyeing is achieved.
Transperse Transfer Printing Dyes - Your best choice for transfer printing on polyester and poly blends. Available in 9 intermixable colors.
And don't miss the work of Barbara Barrick McKie at http://www.mckieart.com/!
>
**I have never done any of my polyester this way. It is all direct application of dyes, either regular or thickened, allowed to dry and heat pressed. The thickened dye is more frugal – all the color is on the ‘right’ side (important with NuSuede), with the back remaining white. I also don’t do heat transfers, because I do 3 – 4 yard pieces and want fairly consistent results. Have yet to do any screen printing – I’ve never gotten into that.
Friday, November 19, 2010
Reviews and Previews
Hard to believe 6 weeks have passed since I last posted. If troubles come in threes, we’ve had it for a while. After the bad brake incident in September, we came home to a hole in the roof, with water running down from the third floor to the entrance hall. Yuck. Got it fixed (there went any profits,) and a couple weeks later the heater started making loud noises and shooting flames. Well, it was about 55 years old, like us, and that’s a pretty long time for a boiler. In the picture at right, the covers were removed for the funeral. It didn’t run like that all the time. Anyway, it got kicked to the curb and a new Energy Star gas unit has been installed. What a difference – and the basement smells much better! Plus, I will have more and hotter water for washing out MX dyes.
We did a total of six shows this fall; still haven’t crunched all the numbers, but it’s time for some other source of income. My current plan is to do the spring shows in Hampton, VA, Somerset, NJ and Lancaster, PA, and then probably no shows except Oaks, since it’s 20 miles away, until (drumroll) Houston, next fall. I spent almost as much to do the show in Chantilly, VA this fall, with the poorest results of any show. It was a good opportunity to have a different set-up (see picture.) The ladies from Quilters Remedy and I had our booths side-by-side, and we each had a cross-aisle next to us, so we both had corner booths.
Thanksgiving is a week away and as always there’s a lot to be thankful for. I’m thankful for all the opportunities that have come my way this year, and all the wonderful people I’ve met along the way. I’m thankful for the optimism necessary to keep trying for a while longer, and for the common sense needed to realize that some sort of ‘Day Job’ is necessary too. I’m very thankful that I won a ribbon at the Oaks show, and have the snow-dyeing article coming out next month in American Quilter! (Both of those actually came with a check!) Now I have to get more work done, including posting lots more fabrics on the website, and upgrading my inventory without spending a lot more money!
Snow Dyeing!
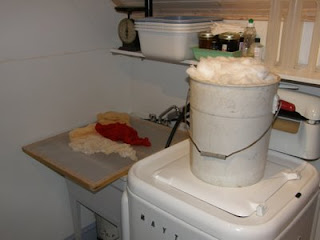




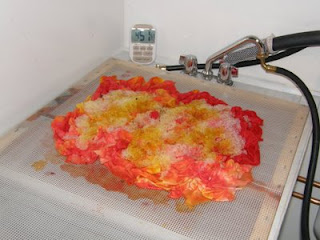

7 comments:
- Deb said...
-
Love the snow dyes! It does make me think I'd like to try and especially love the grid marks from the board underneath!!! I live in the south, so this is a limited opportunity for me. I may get the equipment ready and see if we get a rare snow storm for me to try it. For our usual snow storms check out my recent posting in my blog http://debharwell.blogspot.com/
- Thursday, January 29, 2009 2:51:00 PM GMT-05:00
- Karen said...
-
It turned out great, good job, neat seeing the grid pattern on the fabric. That happened to me once with a golf ball (don't ask).
Karen - Thursday, January 29, 2009 4:09:00 PM GMT-05:00
- Anonymous said...
-
this is cool lisa! i am definitely going to try this out (sooner or later). we have plenty of snow but it is unfortunately buried under a good piece of ice. sort of like creme brulee on a large scale.
Rita from Scranton - Friday, January 30, 2009 8:08:00 AM GMT-05:00
- I'm Bobbie said...
-
Love your pieces! Thanks for your comment on my blog. Yes, I've been to the Barn many times, all of Carol Soderlund's classes plus more. Bet we've been there at the same time.
Keep up the great blog! - Tuesday, February 3, 2009 3:05:00 PM GMT-05:00
- Judy said...
-
lovely snow dyeing.......pity I live in GA where we rarely have any snow at all!
- Sunday, February 15, 2009 10:18:00 AM GMT-05:00
- Sue said...
-
Your fabric is very, very pretty. Thanks for blogging about it. I have a question though. Do you think the results are significantly different than doing low immersion dyeing and really good scrunching? Just curious, as I've not done it.
Sue - Sunday, February 15, 2009 10:42:00 AM GMT-05:00
- Lisa in Penna said...
-
Hi Sue - The finished product is rather different from traditional scrunching. Two of the fabrics were already dyed a very pale orange, but the sateen that started out white doesn't have any white areas remaining. They are pale yellow at the lightest. Also, there isn't the usual crystalline patterning from LWI. All the edges are softer. Jane Dunnewold described this as 'snow resist' dyeing, and I think that the gradual combination of dye and fabric does lead to a different result. I'd like to hear what other folks think! - Lisa
- Sunday, February 15, 2009 9:28:00 PM GMT-05:00
Links to this post
- Färben im Schnee
- 1. Schnee vom Gestern Des öfteren bin ich gefragt worden, ob ich schon im Schnee gefärbt hätte. Gereitz hat es mich schon lange. Gestern habe ich es endlich probiert, Schnee gibt es ja momentan genug. In Quilting Arts Nr. ...
- Posted by Helena at Friday, January 15, 2010 4:50:00 AM GMT-05:00